Who does not use Kanban? This is what ensures that you never run out of toilet paper at home… In industry, Kanban maintains an acceptable level of inventory. This is a technique that is increasingly used in IT services. It helps to finish what is started and deliver value as soon as possible.
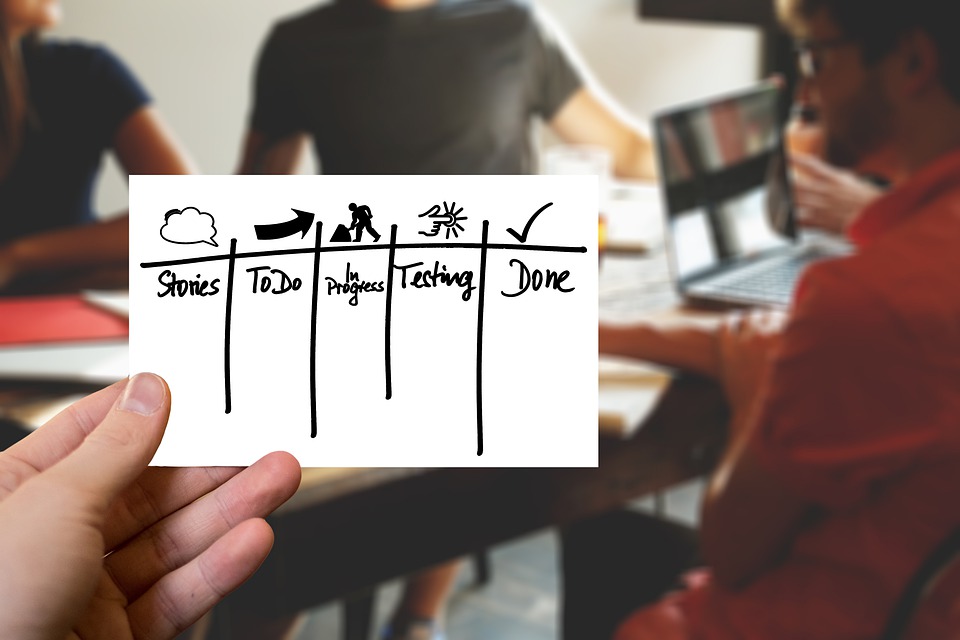
What is Kanban?
Kanban is still a Japanese word: 看板, which means panel. It has been set up formally in the automobile industry, by means of… panels.
The goal is to limit the stock in production. In order to be able to quickly detect an error and correct it, it is necessary to have the minimum of stock between every two stages of production. Conversely, each machine must have upstream stock, so as not to stop producing. It is difficult for the operator to always know the right amount of stock to keep, and therefore to produce, for all references. That’s why the Kanban was set up.
The number of kanban is calculated according to the customer’s request, but especially the processing time on each machine. Each time he takes an item in the stock, the worker makes the Kanban to the previous workstation, which can then initiate the production of a new item.
Concretely what does it look like?
Depending on the size of the parts and the type of production, the Kanban can take several forms. First of all, it is a label affixed to the piece. The operator deposits it in a box that is regularly collected. In the more modern version, it is a barcode that he scans. The Kanban is digital to accelerate communication and keep track of production.
In stores, labels are sometimes placed to help staff order out-of-stock items. It’s the same principle.
It can also be a tray or a trolley. The operator empties the trolley or the bin, then places it in a dedicated area. It can finally be a physical location, delimited by markings. The 5S are a prerequisite for the implementation of Kanban, because in order to function well, one must clearly define each zone.
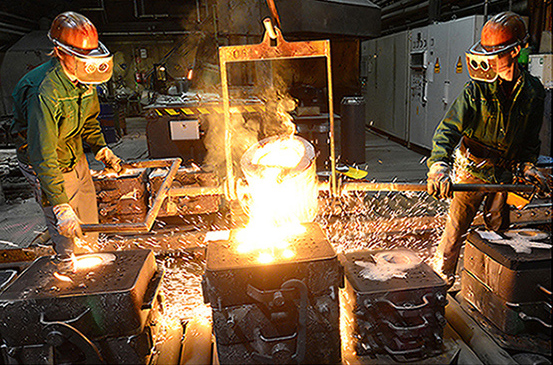
You use Kanban every day (or almost)…
At home, the simplest Kanban is that of toilet paper: you have a roll in use. You probably have a stock of a few rolls nearby. You may have a secondary stock in another room. This “central” stock supplies all the bathrooms of the house.
You know (even if there are no labels or a zone delimited by a ribbon) when you have to buy more: when the central stock is almost empty, but not too much… You know your consumption and know if you have to buy more when there is 1, 2 or 5 rolls left in your central stock.
But why use this method?
You don’t want your house to be cluttered with toilet paper neither to run out of it. The Kanban maintains an acceptable level of stock or WIP (for work in progress): neither too much nor too little.
Too much stock or work in progress generates costs and risks: rework in case of error, financial immobilization. Conversely, a lack of inventory generates costs related to underutilization of resources. Well dimensioned, the Kanban maintains the optimum level.
And in the service world?
This is the new use of Kanban. It counters our natural tendency to start a lot of things and not finish them. In resonance with Agile principles, it contributes to deliver complete things. If I start a task, I have to finish it before I start another one. If the items are well prioritized, then I quickly deliver the added value to my client.
The principle is the same: the work to be done is divided into tasks, which take the form of cards. They are usually recorded in software such as Jira, Trello or Monday. Each task is then assigned to (or selected by) a team member. The number of tasks is limited to 3 or 4 most often. The goal is to be able to deliver, so finalize, the task in the day or three days.
This ensures the group keeps a certain momentum. When using Agile principles, tasks are not treated as queues: FIFO (first in, first out) or LIFO (last in first out), they are processed according to their priority. The Kanban helps to use this principle.
In fact one can define Kanban by individual or by stage of production. For example, no more than 3 items at a time in quality assurance. Thus, the team can decide to start longer tasks, if the quality assurance and the previous step are already well loaded.
The personal Kanban
It’s simple! On a sheet of paper, draw three columns: to do, in progress and done. The “in progress” column must contain three or four post-it maximum. The column “done” underlines the work accomplished, the column “to do” motivates you to finalize the small details of a task to be able to embark on another project!
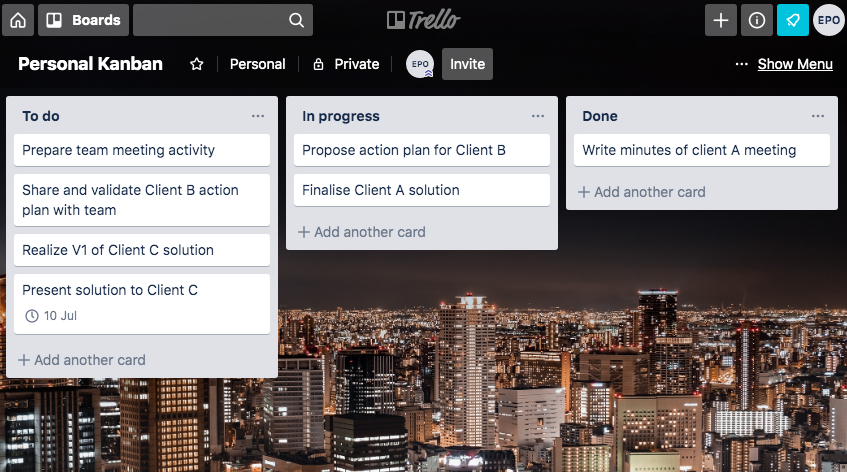
How many project tasks do work on in parallel? Would a simple personal Kanban help you finish what you started?