Have you ever built a house or worked on a construction site? If so, you know it takes a long time. Besides, there are mistakes. A lot of constrcution materials are wasted. Coordinating all the trades can become a nightmare. Add in the mix that quality is not at the expected level. And finally, it’s quite expensive.
Lean and Agile principles apply in all business sectors, and can improve houses building and renovation.

How improve the construction of buildings?
Once you have noticed the problem, what should you do? How to optimize construction processes to improve quality, reduce costs and delays? You just have to draw inspiration from the best practices in the world, and industrialize the construction process.
It is in Germany we should take a look. It is the cradle of manufactured panelised building system. In New Zealand, Concision is entering this market with the goal of revolutionizing and improving building construction.
First of all, it is important to remember that construction is a craft. The craftsmen succeed each other on the site. They each carry out their work according to their expertise. Every building site is different. But in the end, the houses all look a little bit the same. Similarly, the larger construction sites have structures that are repeated.
Each of these craftsmen can improve. The organization of the construction site can also be improved. However, since houses have been built for centuries, the majority of optimizations have already been achieved. The tools are mechanized and the materials simplified.
Industrialize and standardize
To go further, it is necessary to industrialize: to prefabricate the houses in factory. As we have already done for clothing, tools or more recently all consumer goods. It is possible to industrialize while maintaining a high level of quality.
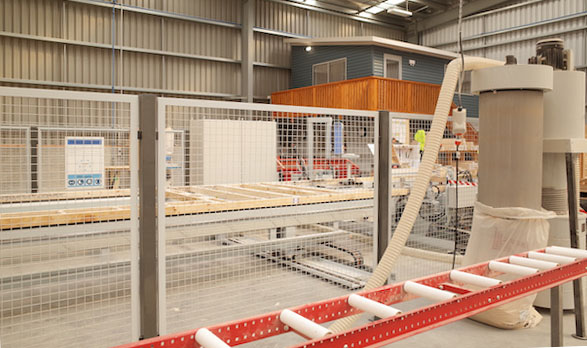
With the exception of a few countries, the majority of buildings are made of wood or steel structure, covered with panels. To industrialize this type of construction efficiently, there are several principles to respect:
- DFMA: Designing For Manufacturing and Assembly
- Standardize
- Communicate between the different trades
- Use the lean principles in the factory.
Why spend more time designing?
This idea is revolutionary in the construction industry. Once the plans are completed, the workers are used to adjusting, correcting, repairing on the construction site. Spending more time in design seems like a waste of time.
Indeed, there is nothing concrete at this stage. However, by knowing the industrial constraints, costs can be reduced. For example, if industrial equipment can make 12 metres long panels, then 12 metres walls must be designed, or that add up to a 12 metres panel. Reducing the amount of “wasted” materials also reduces the environmental impact.
Then you have to decide how much integration you want. Thus, it is possible to install all the networks (water, electricity, telephony) in advance. In the factory, the wall is a board accessible from all sides. This configuration makes mounting easier. The downside is an increase in design work. It is also more complicated to change during construction.
This is an important change for customers. Instead of walking around a partially built house and indicating where they want their electrical sockets and switches, they need to do it on a plan. Virtual reality could help customers better visualize and decide.
Standardize plans
As I mentioned earlier, standardisation is the basis for mass production and cost reduction. Unfortunately, although it is financially interesting to build a single model of school or gymnasium, everyone wants a unique building that testifies to their identity.
It is possible to build residential quarters, based on two or three models of house. On the other hand, everyone will want to modulate the interior space, choose the location of the sockets.
Because a lot of work is done upstream, changing plans for each client means significant costs.
The main question that arises in the industrialization of construction is how far to standardize. What choices should be offered to the customer, to personalize his building, to meet his needs, while maintaining a high level of industrial integration?
Communicate between the different trades
As in any industrial process involving different stakeholders, communication is key to success. This starts with the use of common protocols for file sharing.
For example, the steel structure manufacturer makes its plans. Instead of sending them directly into production, he shares them with Concision, which makes the walls. By superimposing the two drawings, we immediately see the collisions. Everyone can then work on changing their design, and then redo the calculations to make the assembly perfect. This avoids the need to cut or adjust on the site. The structure therefore has the expected resistance.
Following discussions with carpenters and masons, Concision changed the organization of the walls in the truck. This speeds up on-site construction. They also interact with plumbers and electricians, to facilitate their work when the panel does not have built-in fluids.
Use the toolkit of operational excellence
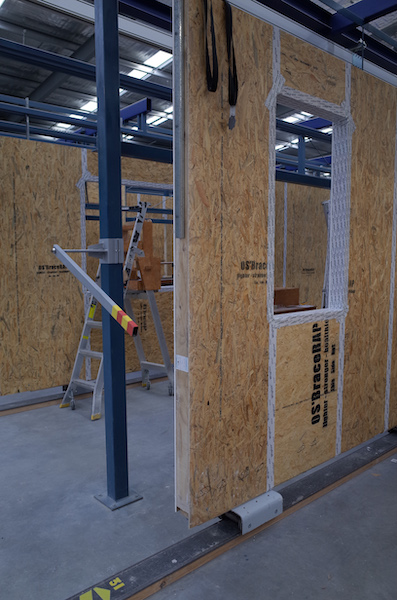
Finally, all lean tools can be used to improve even more. For example, the poka-yoke concept makes it easy to assemble the panels. By pre-drilling holes in the right places, carpenters can’t go wrong on the job site.
The 5S are of course deployed throughout the assembly plant. The work is standardized on each workstation. Finally, the employees are polyvalent, in order to facilitate the smoothing of the load on each station.
A way forward to improve construction?
Is the market ready for prefabricated and standardized homes? Concision makes the bet that it is by proposing new products, that the market will evolve. The past and the industrialization of the construction market in Germany make them right.
To improve a process that already seems optimal, we need to look further, to other industries or other countries. Finally, it is important to innovate and revolutionize its market.