In order to reduce waste in services, it must be made visible. Unlike the industry, bottlenecks are often virtual. It requires some imagination to identify them.
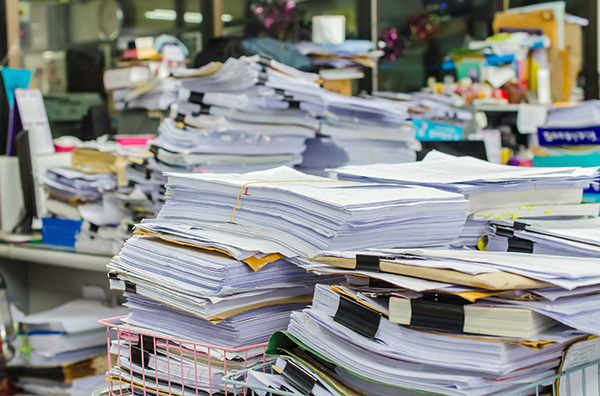
Lean and Six Sigma concepts are very much oriented towards manufacturing. In IT, Agile techniques are very similar both in terms of concepts and tools. This also applies to the service sector, with some adjustments. I recommend reading the book Office Kaizen by William Lareau, which goes through most of the tools and methods and explains them in the service industry.
Physical or virtual production?
Ultimately, service firms produce value, but through intellectual rather than mechanical processes, which causes two difficulties compared to manufacturing:
The notion of flow also applies since the information or request follows a flow. However, the flow is often immaterial and more complex to follow: the value chain is less visible in offices than in a factory. Flow-related waste is less visible and more insidious to track down, as it can take on several dimensions. The efficiency of a service organization will mainly rely on the simplicity and relevance of these flows.
The other difficulty lies in the nature of the human. Indeed, unlike a machine, its operation is not always repeatable. Man lives from moods, from fatigue. The TPM is less applicable. More generally, the functioning of the human brain is not standard. This is the very nature of service companies: to distinguish what can be standardized (and therefore automated) from the value brought by the human being in the value chain.
What is waste?
Wastefulness includes all the actions, the steps that the customer is not willing to pay for in order to obtain a service.
Here are some examples:
- the time it takes to find a document
- triple signature for approval of an application
- different answers to the same question by different people
- an error
- waiting for service
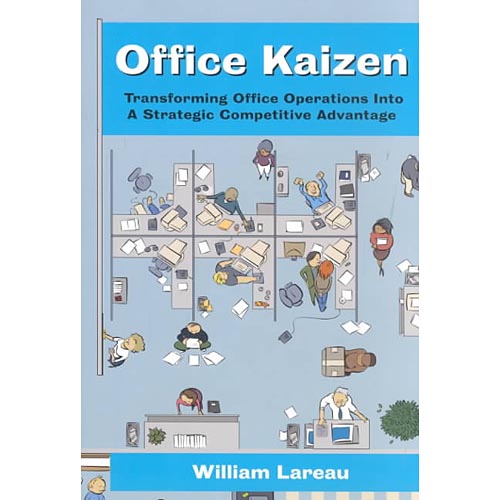
In his book Office Kaizen, William Lareau classifies waste into 4 categories and 26 sub-categories. There are therefore many variations, but they all lead to the same result: the customer pays for an activity that does not add value to the service provided.
How can we eliminate waste?
In order to eliminate it, it must be identified. Easier said than done… I have suggested some techniques to highlight them.
Then, see how the waste can be eliminated or at least reduced, the 5 Whys tool is your most valuable ally in this step, as it will help you find the root cause.
- Why do three people have to approve the application?
- For what reason(s) can X not sign alone?
- Why does Y want the information?
- …
The 5 W’s can also be used:
- Which archiving rules apply to which documents?
- Who really needs … ?
- Where should the information be?
- When should we … ?
Finally, mapping (when different sectors are impacted) is a good starting point to imagine the ideal process. It should have as few steps and interactions as possible.