I had the chance to participate in the first “Colloque Lean de la Santé et des Services Sociaux” on January 26 and 27, 2012 in Orford. While the road to improvement is long and the challenges are great, I have met with healthcare executives and managers who are convinced that continuous improvement and the lean philosophy are the way forward for the management of their services.
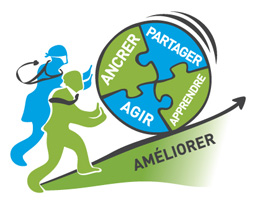
This conference was organized by the Virtual Community of Practice in Continuous Improvement. The objective of this conference was to share and create links between health care institutions. A few months ago, the Quebec Minister of Health, Yves Bolduc, asked all health service centers to apply the “Toyota method” to improve their processes. Beyond the simple words and methodology, this conference was an opportunity for participants to share around this theme and to better understand what the methods inspired by the Toyota model could bring them.
A conference focused on sharing best practices
The workshops and keynotes were of a very high level. We have had examples of hospitals applying these methods for several years:
- Thedacare in Wisconsin
- St. Boniface in Manitoba
- A team from the CHU Mont Gondinne in Belgium, came to present us what they experienced in their first two years of “lean”
- A youth center that started the process just over a year ago also shared its experience.
The presentations were training oriented: what worked, what doesn’t work as well, how we could have done better,… At each conference, the philosophy and some tools were also presented. Although I know the tools, methods and philosophy, I was fascinated by the charisma of the speakers and the examples given. In parallel to the conferences, 4 workshops regrouping about twenty participants offered more concrete and interactive exchanges.
I was impressed by the large number and variety of participants. We were 184 people from 54 health institutions (including 2 outside Canada). There were 61 professionals, 42 managers and 81 directors. Participants were attentive and asked many questions of each speaker. In the discussions I had with some of the participants, I felt all the interest, but also all the questions that this approach brings.
Lean, a cultural change above all
One of the conferences also raised the pertinent question of the distinction between “doing” lean and “being” lean. This issue is as important for hospitals as it is for industrial or service companies. Anyone can do a lean project. The tools are known and well documented. A book, a training and everyone can apply and do 5S, SMED or even a Six Sigma project. For this reason, the speakers emphasized the key success factors. Indeed, success depends on organization and culture more than on technique. It is good to see that in order to implement continuous improvement in the health sector, the focus is on changing the culture and the organizational model. The points that stood out the most were:
- management commitment,
- clear objectives and priority management,
- listening and respecting the field, where the experts are.
Several speakers spoke about the Gemba, a Japanese word meaning “where the action is” which could be translated as “ground”.
Be lean, involving everyone
If doing lean is easy, being lean requires much more effort but also brings more results. Because at Thedacare, which is lean, 6000 employees are dedicated to continuous improvement. A team of 24 people support them and carry out projects. But on a daily basis, everyone is responsible for continuous improvement. This gives much better results and makes the actions more sustainable. This hospital started the process about ten years ago. It takes a long time to get to this level of integration of the continuous improvement culture. This is a goal that every start-up company should set for itself. This objective will be planned in the long term, but from the very first projects, the involvement of teams, the training of managers to accompany field staff in their autonomy and the day-to-day management should be thought out.