In an ultra-competitive world, all companies want to achieve the best balance between costs, quality and deadlines. In industry, quality at low cost can ultimately be expensive. That’s why the poke-yoke is so often used.
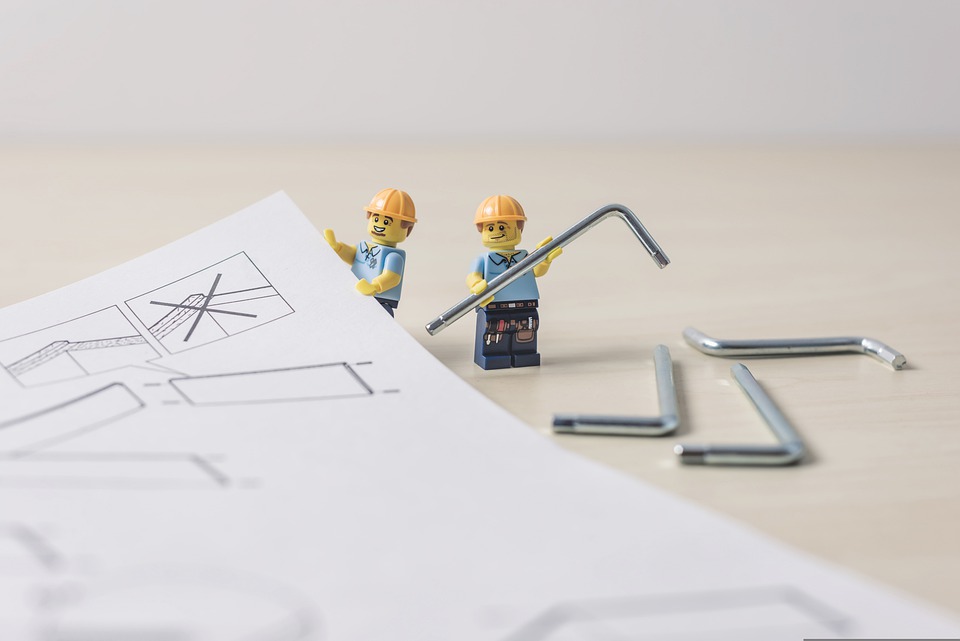
When assembling parts manually, how can you guarantee that the operator always mounts the right part in the right place? This is the purpose of foolproofing, also called poka-yoke.
Poka-yoke, is that a cold or warm japanese meal?
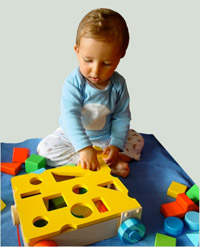
The concept behing is simple… From a young age, we learn this principle. As in this toy, each piece can only go to one place, the “right” one. Poka-yoke is a preventive method, implemented upstream to prevent errors.
Poka-yoke systems should be designed as simply as possible, to ensure that all parts are right. It replaces a 100% control measure.
If each part can go to one place in one way, there is no need to check that it is done properly.
This principle applies of course to manufacturing, to optimise operations and get it right first time. But it is also useful for the user. The coding helps the user to use the product properly. You make it easier for them.
How to prevent users from getting it wrong?
There are two main methods: mechanical and visual. Mechanical coding is more reliable than visual coding, but more complex and more expensive to implement. It is, in general, reserved for the most critical cases, when an error may have an impact on the security of property or people.
In the industry, the mechanical coding can take place in different ways:
- Differences in size or shape
- Adding a protrusion to a specific location
- A different fastening system for each piece
- Spring or lever activated by the part
For example, the USB connection is mechanically error-proofed. You cannot plug a USB stick in backwards or into the wrong connector.
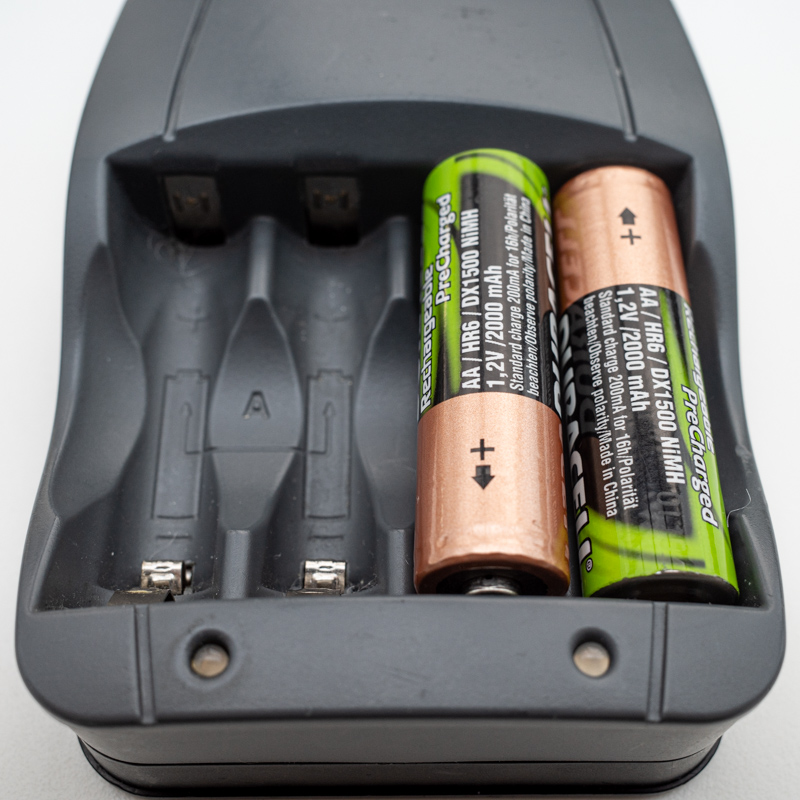
Batteries are another interesting example. Whilst the polarity is physically different, we usually see visual coding in products. Indeed, it is easier to print a plus or a battery shape than to make sure that the battery can only go one way.
On the other hand, the battery chargers rely on mechanical coding. You can try, but the battery can’t clip on and load upside down. We are exactly in the case where the risk is too great for visual distortion.
The choice between a visual or mechanical poka-yoke will be based on the risk of error, impacts for the customer and cost.
The coding system can be implemented at different stages of the product life cycle: during the design, during industrialization or during a process improvement activity. It is obvious that a product designed with the foolproof system is always the least expensive solution. However, simple solutions such as jigs or color codes can be implemented during a continuous improvement process. In addition to the anti-error aspect, this type of system reduces the cognitive load of the operator and intellectual fatigue, sources of stress.